Mechanical fasteners like screws, nuts, and bolts are fundamental components in any machine or vehicle. In this video, we will walk you through the basics of:
- Different fastener types and shapes
- Drive types
- Materials and coatings
- Galvanic corrosion
- Coarse vs fine thread
- Best practices of joint design
- Helicoils and heat-set inserts
- Calculating the correct preload and torque
- Vibration control methods
And we’ll answer that age-old question: what’s the difference between a screw and a bolt?
tarkka Design Charts
Additional Resources
- NASA, Fastener Design Manual
- This manual provides a comprehensive explanation of fastener types, materials and coatings, joint design, and vibration control.
- AISC, Guide to Design Criteria for Bolted and Riveted Joints
- This document describes the requirements and theory of a variety of bolted joints used primarily in structural engineering.
- Unbrako, Engineering Guide
- Unbrako is one of the larger manufacturers of socket head screws, and their engineering manual consolidates most of the dimensional and mechanical specifications from the ASME and ISO standards.
- US Department of Defense, MIL-STD-889C: Dissimilar Metals
- This is an excellent resource for understanding and managing galvanic corrosion in both freshwater and marine environments. It is one of the few documents that includes a galvanic series with modern alloys and coatings.
- Sandia National Laboratories, Guideline for Bolted Joint Design and Analysis
- This guideline goes into more detail about both closed-form and FEA approaches to fastener analysis. It also describes how to analyze fastener fatigue.
Case Studies
- Australian Transport Safety Bureau, Embrittled Nut and Related Failures Robinson R22 Beta Helicopter VH-JNP
- There were several aviation accidents involving embrittled jet nuts, but this report is the most detailed.
- FHWA, Ft. Pitt Tunnel Luminaire Connection Failure
- This report discusses a failure of tunnel light fixtures in Pittsburgh, PA due to galvanic corrosion. The stainless steel fasteners caused accelerated corrosion of the aluminum base metal.
Video Transcript
Fasteners are some of the most important components in any machine, but they are often taken for granted. It is vital to correctly choose and use them, or else the mechanical integrity of a product is at risk and there can be devastating consequences. Thread type, preload, material choice, coating spec, drive selection, and more, all need to be understood and applied properly. In this video, we are going to go over all these fastener topics and many more, so that you know the nuts and bolts of nuts and bolts.
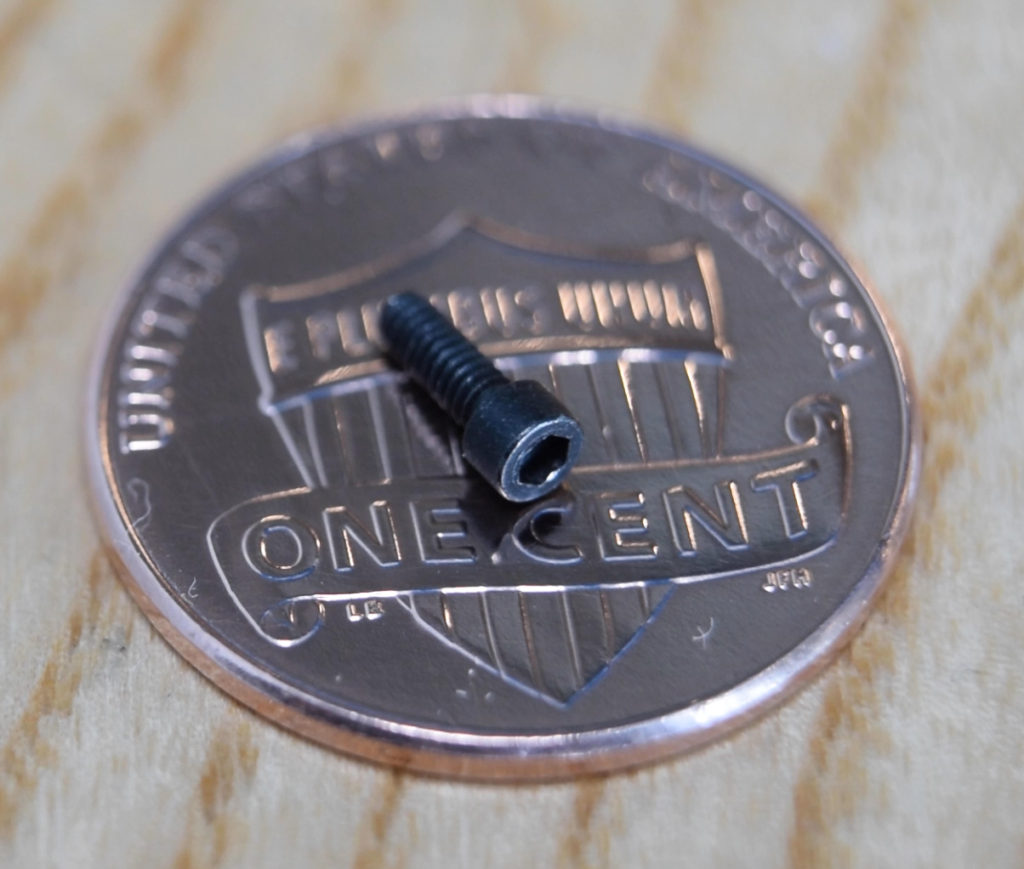
Fasteners come in a wide range of shapes and sizes, from the tiny microscrews used in electronics to the large structural bolts that hold buildings together. The vast variety available can be a bit overwhelming, but we’ll show you a few of the most common types and talk about where they’re best used.
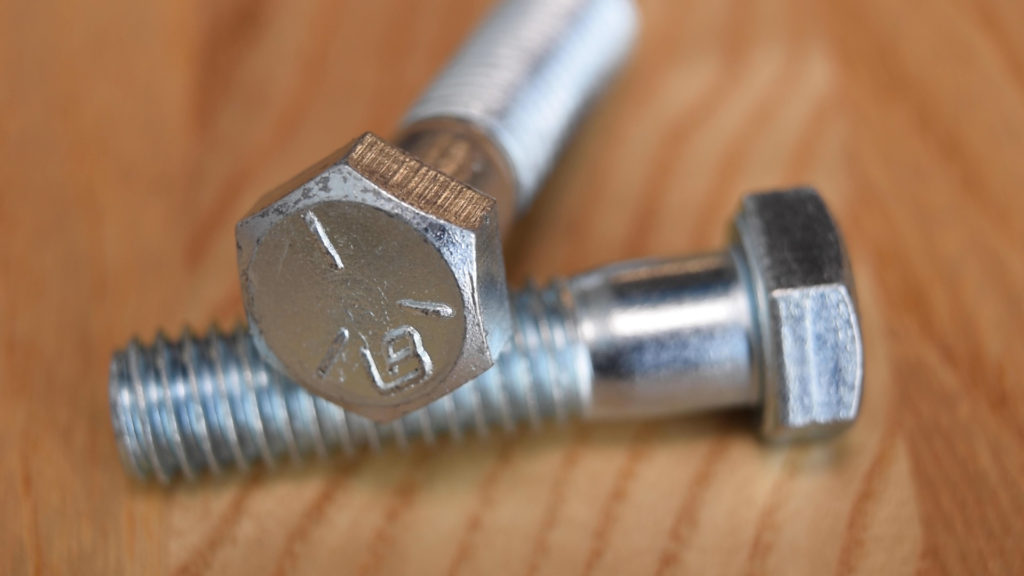
These are hex head screws, which most people informally call bolts. Because they’re cheap, strong, and easy to work with, they’re probably the most common fasteners you’ll encounter. The only trade-off is that because these require a wrench or socket to tighten, the designer has to leave a fair amount of room around the fastener to accommodate the tool. If you’re designing with these, you can reference Machinery’s Handbook for a helpful table on tool clearance requirements.
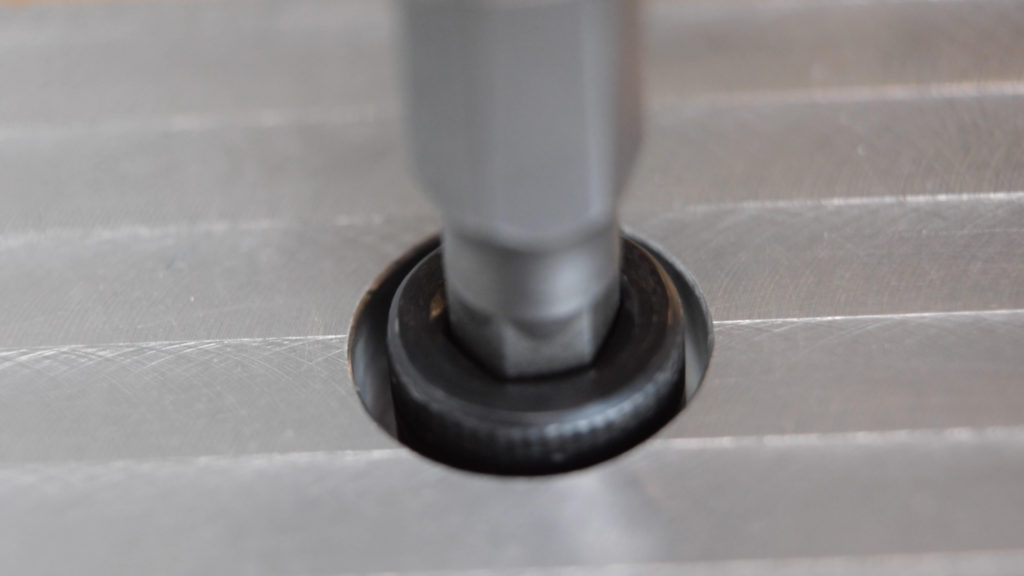
In situations where space is at a premium, you might consider a socket head screw. Since they’re driven from the top, you can place them in tight spots, or bury them in a counter bore. Low-head screws and button heads have a lower profile and are often used in electronics. A flat head screw can be recessed inside a countersink and is great when you need the head of the fastener to sit below the surface of thinner materials.
Screws are most commonly sold with a hex drive, either external in the case of hex head cap screws, or internal in the case of socket head cap screws, and this is perfectly fine for larger fasteners. For smaller fasteners, below maybe #6, hex drives strip out very easily, and you should consider a more robust drive like Torx. High-strength nuts and screws are sometimes manufactured with an external 12-point drive, which offers more points of contact than the traditional 6-point hex.
It’s best to avoid Phillips and slotted drives if you can. While being widely available, they are subject to “cam-out” and can strip easily. Even the construction industry is moving to Torx drive because of the many advantages.
There’s also a lot of really odd-ball drive types that were designed for very specific applications, or to purposely be obscure. Unless your design fits into these categories, you should probably consider something more mainstream.
You may be wondering what the difference is between a “screw” and a “bolt”. Technically, the difference depends on how the fastener is used, not the actual fastener itself. Bolts are used with thru-holes and are fastened with a nut. Screws are used in tapped holes. Screws have a Design-for-Assembly advantage since the technician only needs to use a single tool to fasten the joint.
Screws are most commonly made from either low carbon or alloy steel, but you will also find them made from stainless steel, titanium, Inconel, brass, and aluminum, or even plastics like nylon or PEEK.
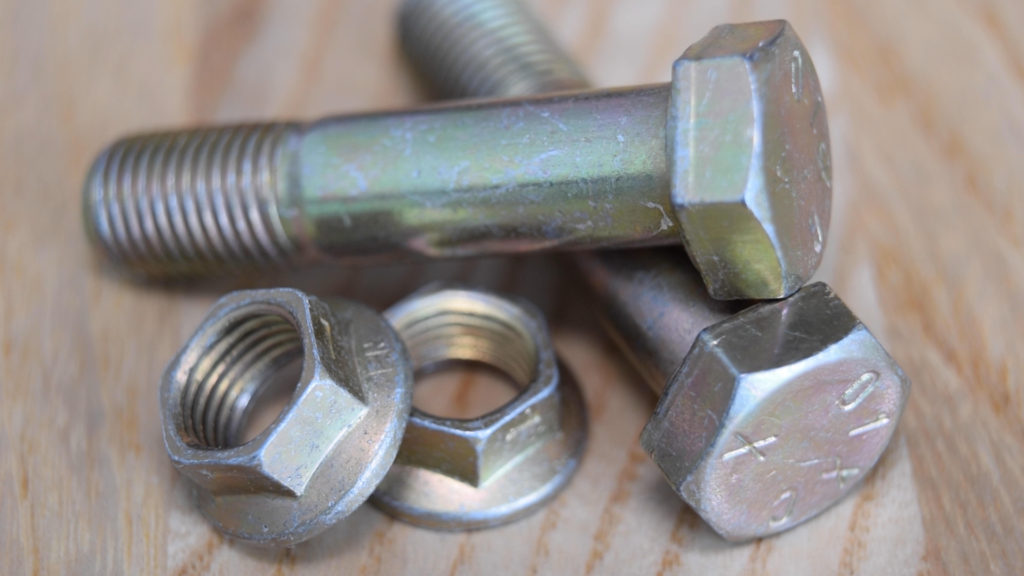
The primary considerations for selecting a material is strength and corrosion resistance. The strongest fasteners are usually made from heat treated alloy steel, but steel will corrode when exposed to moisture. Coatings are commonly applied to alloy steel fasteners to make them more resistant to corrosion.
Zinc plating is economical and is the most common coating on low and medium strength fasteners. It is sufficient for dry environments that receive only occasional contact with moisture. Grade-8 screws usually receive a yellowish chromate conversion coating which has slightly better corrosion resistance than electroplated zinc.
Fasteners that will be exposed to the elements are often galvanized. This means that the raw bolt is dipped in a pot of molten zinc, which adheres to the base metal. This process is sometimes nicknamed “hot-dipped” and the resulting coating is much thicker than the electroplated zinc. Galvanized fasteners are typically acceptable for exterior installations.
Aerospace fasteners are usually plated with cadmium. This is a very effective coating, but cadmium is an extraordinarily dangerous material, and these hazards are compelling manufacturers to find safer alternatives.
Some fasteners, particularly socket head cap screws, are coated with black oxide, and while it looks nice, this doesn’t significantly improve the corrosion resistance over bare steel.
Coatings are generally not sufficient for applications in which the fastener will be immersed for extended periods. Switching to a stainless steel fastener made from an alloy like 304 or 316 improves the corrosion resistance, but 300-series stainless is not nearly as strong as alloy steel. If you need both high strength and corrosion resistance, you may need to use a super alloy like A286 or 17-4PH. Nickel-based alloys like Inconel and Hastelloy are used in the most demanding applications.
Material and coating specifications are defined by standards, such as ASTM, NAS, AS and SAE, or the former “MIL” and “AN” specs. Metric fasteners are defined by ISO or DIN specifications. Various grades of fasteners are sometimes defined by the standards, and for hex head screws, the grade is usually designated by marks on the heads. Metric fasteners use a system of numbers stamped into the head. In either case, the higher the grade, the higher the tensile strength of the fastener. Alloy steel socket head cap screws generally have a strength similar to grade 8 bolts.
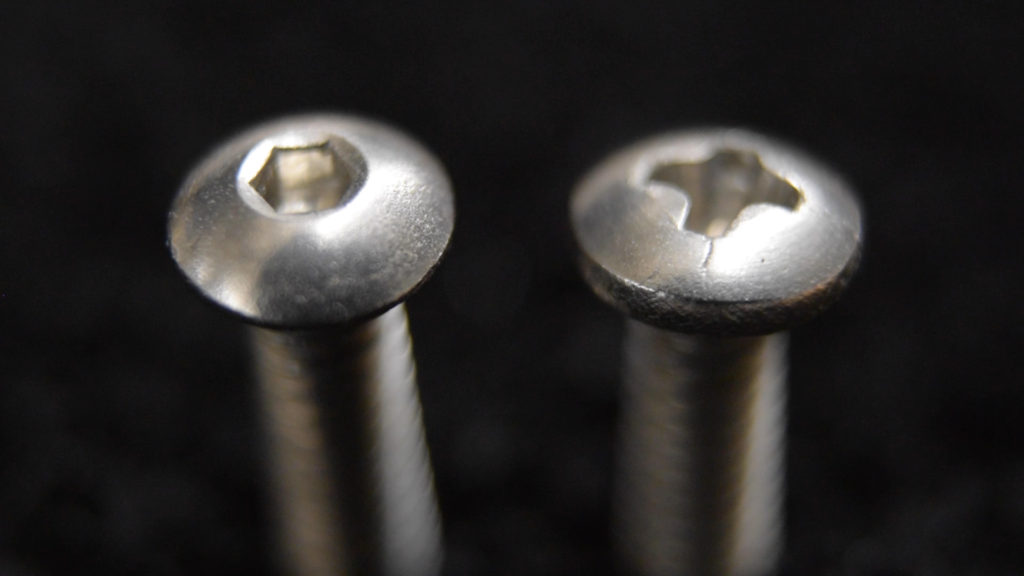
It is important to ensure that the fasteners you are purchasing conform to the required specifications for your product or industry. For example, you may have seen screws like this at the hardware store, where they are typically labeled as “pan head” screws. Dimensionally, they are very similar to button head screws, and both are made from steel and zinc plated. However, the hardware store screws are made from soft carbon steel, while the button heads are made from heat treated alloy steel per an ASTM specification, and are over three times as strong. For some projects, hardware store fasteners are fine, but for critical applications, purchase fasteners from a company like McMaster-Carr that lists exactly what specifications they conform to.
Fastener materials and coatings is a hugely important area, especially in industries like aerospace, marine, and energy. A particular point of concern is hydrogen embrittlement. During the plating process, hydrogen is often produced which can become trapped inside the metal’s crystal structure. This causes the steel to become brittle and susceptible to spontaneous failure. There was a rash of aviation accidents that occurred when MS jet nuts that had hydrogen embrittlement failed in service. In the corrosive environments common in the marine and energy industries, stress corrosion cracking can cause similar, spontaneous failures.
Another consideration is galvanic corrosion. When materials that are far apart on the galvanic series are in contact in the presence of an electrolyte, a galvanic cell is formed. In this case, accelerated corrosion occurs on the more anodic material. If the anodic material happens to be small or thin, this corrosion can be extremely severe.
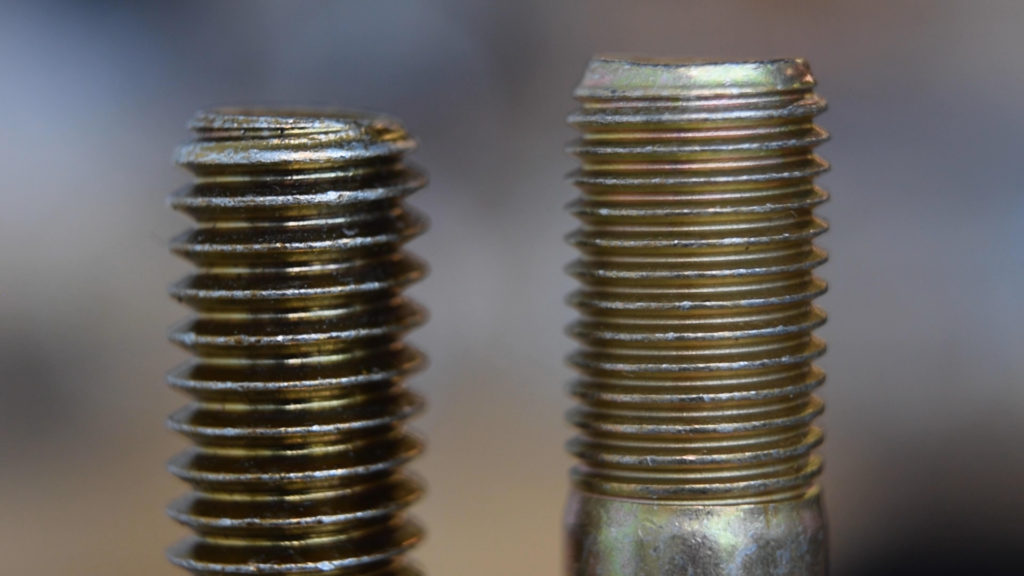
Fasteners are available in both coarse and fine threads. Coarse thread fasteners, conforming to the UNC thread specification, have fewer threads per inch and are generally the first choice. However, fine thread fasteners are used in high-performance applications like aerospace and automotive because they have several advantages. Size-for-size, fine thread bolts are about 10% stronger than coarse thread bolts, and the lower helix angle makes them more resistant to vibration. However, they are easier to cross thread and don’t tolerate debris or thread damage well.
A slight variation to the UNF and UNC standards is the J thread type. Instead of the root of the external thread being a sharp V, the J thread type has a prescribed root radius. The radius helps improve fatigue performance for cyclically loaded screws. You typically only see this type of thread in aerospace.
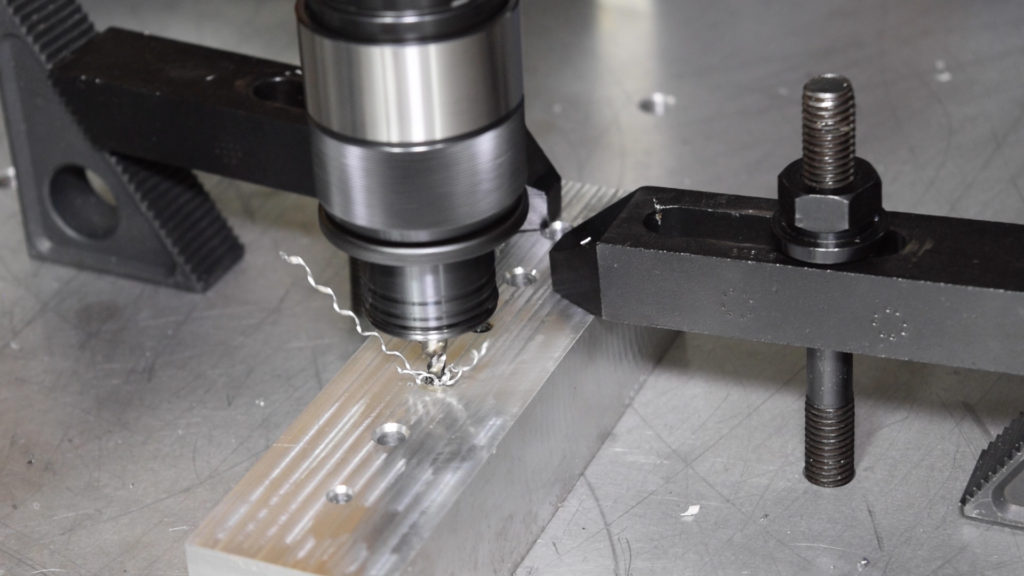
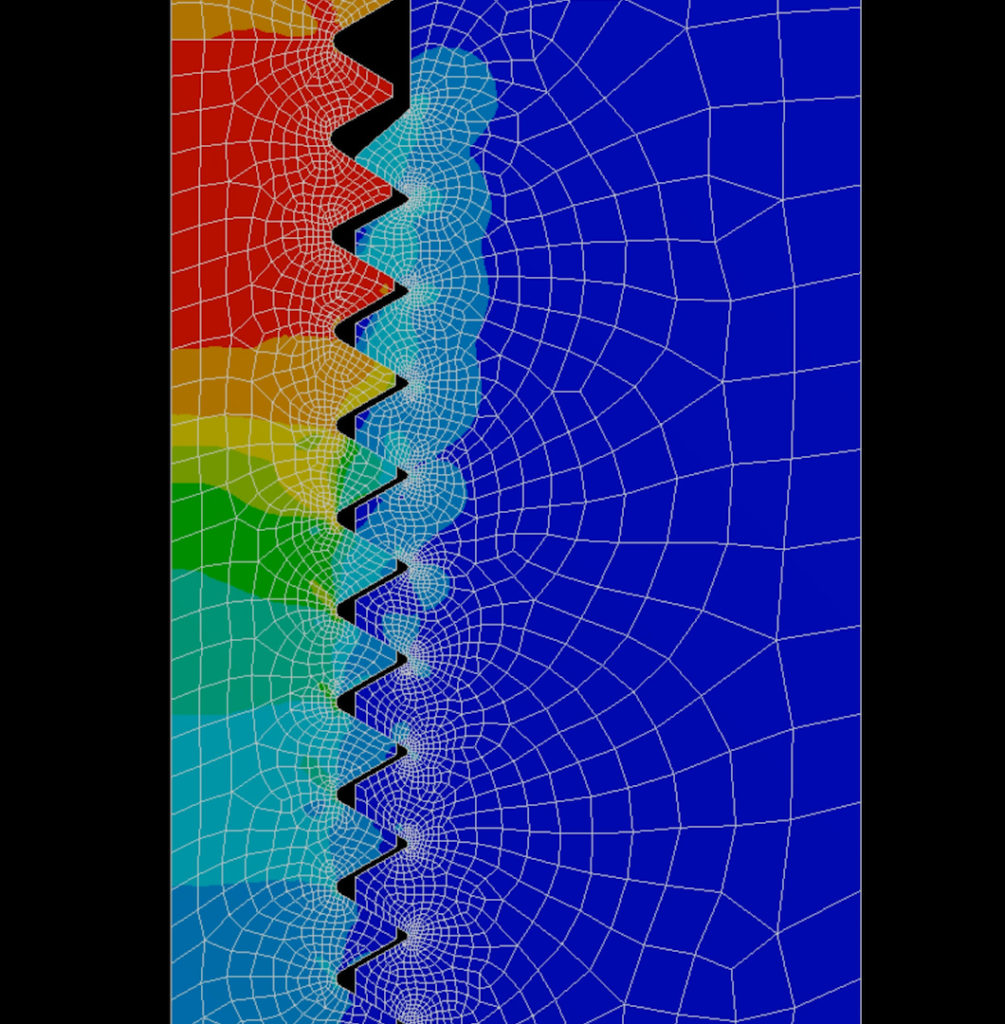
When designing tapped holes, you need to have enough thread engagement to allow the bolt to be fully tightened to its tensile limit. For threads in most metals, a thread engagement length of around two times the nominal size of the screw is sufficient. An interesting nuance of threaded holes is that they don’t share the tensile load evenly along their length. In this FEA, we’re simulating tightening a steel screw into an aluminum tapped hole, and you can see that the first few threads do almost all the work. Once you get beyond about the eighth thread, there is almost no load being carried. Hence, there is little benefit to additional thread engagement, and it simply adds to the assembly time.
If the tapped threads in a workpiece ever become damaged, you can use a component called a helical insert (often sold under the tradename Helicoil) to repair them. You drill out the original thread with a drill that is larger than major diameter, and use a special tap to cut new threads. Then, you install the insert with a threaded mandrel, and break off the tang at the bottom.
Sometimes people will install Helicoils in brand new parts, especially those made of soft materials like aluminum or magnesium. This won’t necessarily make the thread any stronger, but it will make it a lot more durable if you will be removing and replacing the fastener frequently.
If you need to thread machine screws into plastic, especially 3D-printed parts, heat-set inserts create a strong, durable thread. There is typically a special tip that you install on a standard soldering iron, which slips inside the insert and allows you to press it into the plastic.
You should do your absolute best to avoid subjecting screw threads to significant shear loads. The decreased area at the root of the thread makes this the weak part of the fastener, and the threads bearing on the mating pieces will lead to fretting. Instead, it’s best to transmit shear loads with dowel pins or shear bosses.
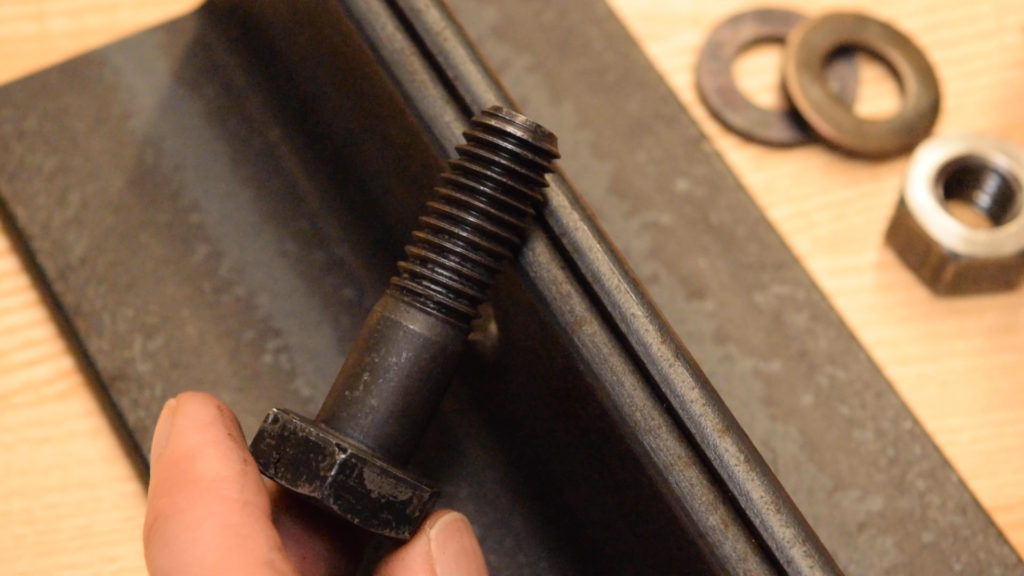
But if you look at any building built from steel, you’ll find thousands of fasteners in shear. Why is it okay there? Structural bolts have an unthreaded section of a controlled length that acts as a dowel. The shearing plane intersects this dowel section, instead of the screw threads, creating a very simple but sound connection.
In cases where you need a fastener to also precisely align components, you might consider a shoulder screw. They have a precision ground shank under the head that can be used as a pin, shaft, or linear guide, and they’re a common component in punch and die assemblies. Shoulder screws usually have a much smaller threaded section than other screws, so you can’t use them to generate a lot of clamping force. Also note that they’re not nearly as strong in shear as a dowel pin, so you shouldn’t subject them to heavy loads.
Washers are used to help spread the bearing stress of bolts and nuts over a wider area. This is important if you have a loose clearance hole where only a small portion of the bolt head would be in contact with the joint members. Washers also reduce marring of the parts and make torque values more reliable.
It’s generally best practice to use a washer under the head of a hex head screw, as well as the nut. Washers are not often not used on socket head cap screws, but to get away with this, it is important to specify a close fit on the clearance hole.
An alternative to a free washer is a flanged screw or nut. These are preferred on mass-produced products to eliminate the handling time of a separate washer.
In practice, vibration is the biggest problem for bolted connections in machines and vehicles, and without careful consideration, the machine will literally shake itself to pieces!
Applying the proper preload goes a huge way in improving the resistance to vibration. The general guideline is to apply between 70 and 90 percent of the bolt’s proof load as preload for static joints.
Preload is usually controlled by the applied torque. The only trouble with this method is that most of the applied torque is lost due to friction in the threads and between the head of the screw and the workpiece. The materials, coatings, and lubricants all play a role, and a correction factor, called the k-factor, is used in the torque formula to account for this. However, even when the k-factor is chosen correctly, the torque method is only accurate to within plus or minus 25%.
For statically loaded joints, there is no reason not to apply the maximum preload to the fastener. However, if a joint is loaded cyclically, the fastener may be subject to fatigue, and the preload and fastener material may need to be adjusted to account for the cyclic stress.
Another closely related parameter is the grip length of the screw. This is the distance between the head of the bolt and the start of the thread engagement, and the longer this distance is, the more resistant the screw will be to loosening.
Sometimes preload is not enough to prevent a fastener from loosening, and additional provisions must be made. For bolted connections, lock nuts are extremely effective. The most basic style has a nylon element that is deformed by the screw threads and holds the two together. These are called “Nylocs.”
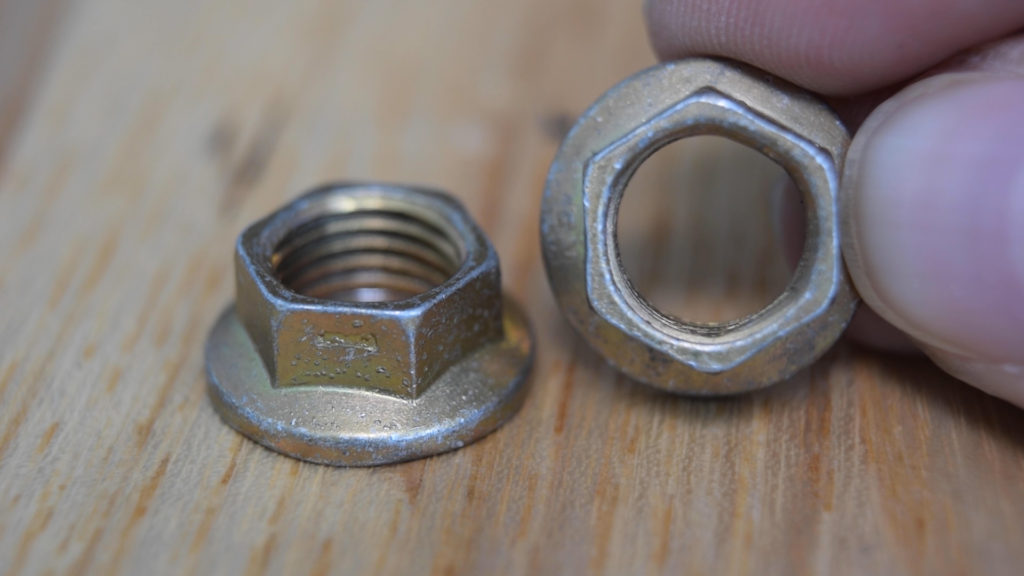
In applications subject to higher temperatures, above about 250 degrees F, the nylon element will soften and not be effective. Instead, deformed thread locknuts are used. These come in a few different styles, but in all cases, the threads are specifically made slightly out of round so that they tightly grip the screw threads.
You may have seen these bent lock washers at the hardware store. These don’t do anything and really have no place in engineering applications.
There are, however, other washer designs that are quite effective. These are called Nord-Lock washers and they come as a two-piece assembly that is glued together. An interlocking wedge feature causes the two washers to separate as the screw is loosened, which actually increases the tensile load in the fastener.
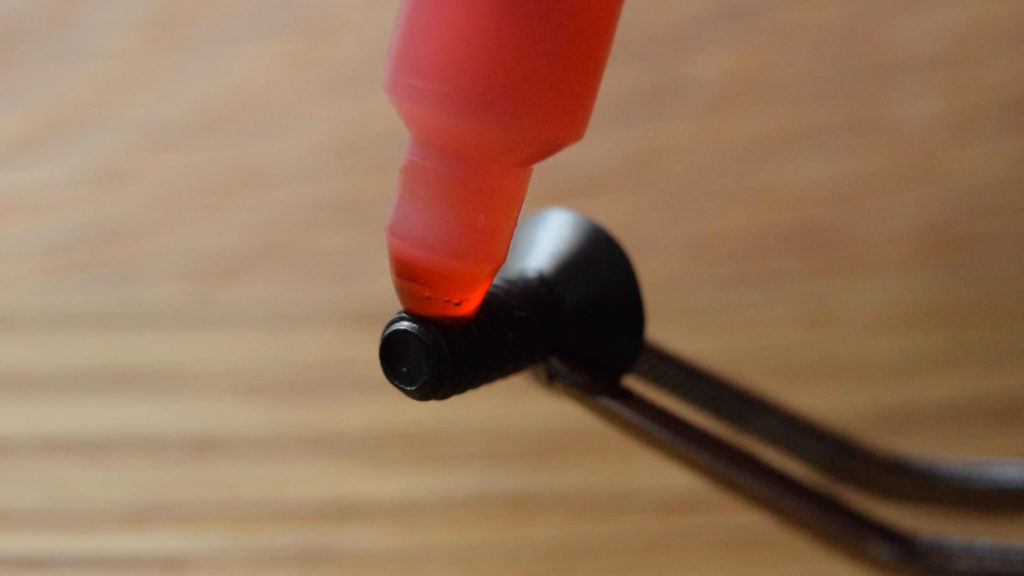
Liquid thread lockers like Loctite are another good option. There are scores of formulations on the market that are designed for different holding strengths, operating temperatures, materials, and thread sizes. Its important to select the correct formula for your application, and fully read the manufacturer’s datasheet. Some compounds require special primers and curing procedures, or only work properly for certain-sized fasteners.
Loctite works extremely well on clean parts and screws, but it is somewhat sensitive to residual grease and cutting oil. It is also difficult to visually confirm after assembly that it has been applied correctly, or even at all.
Mass-produced products often use fasteners with a nylon “patch” that is pre-applied to the threads. This isn’t as effective as Loctite, but is a lot faster to assemble.
There are also proprietary taps that cut a special thread form that is compatible with standard fasteners. The modified thread geometry creates a locking effect that makes the fastener more difficult to remove.
When all else fails, the most effective way to prevent loosening is to physically prevent the fastener from turning after it’s tightened. Aircraft mechanics use safety wire for this, and it’s extremely effective as long as it’s installed properly.
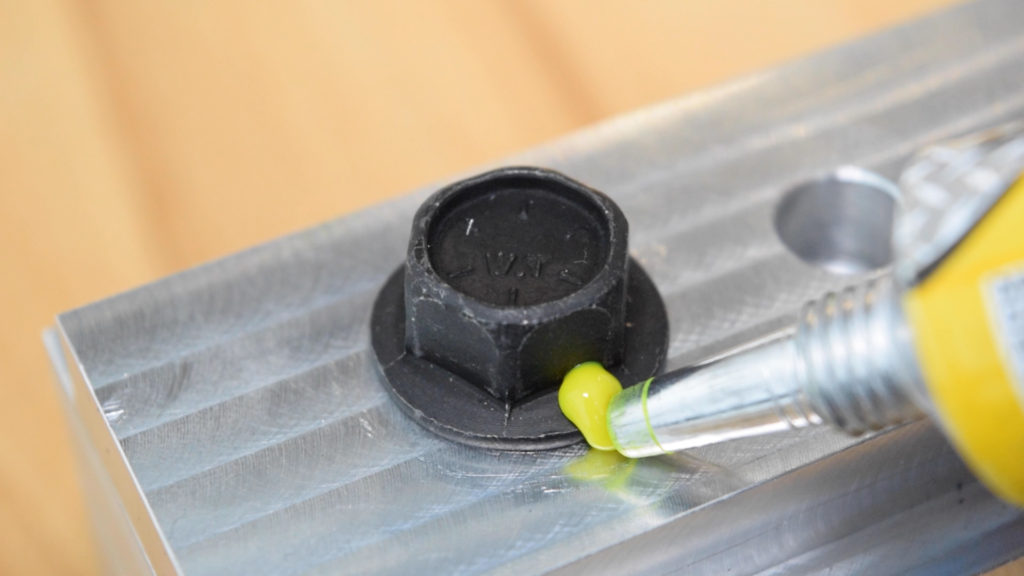
One thing to watch out for is that a fastener that has been properly torqued looks the same as one that is only finger tight. A good practice is to mark the fasteners one-by-one as they are torqued. Then, a visual inspection will reveal which ones were missed. This special marking wax makes it clear when a fastener has been loosened, either by a person or by vibration.
We really appreciate you taking the time to watch our video. We couldn’t possibly cover every type of fastener or design, so if you have a question or something to add, be sure to leave a comment. In the companion blog post, we’ve listed a bunch of additional resources, as well as all the charts we featured in this video.
We have also started an email newsletter with curated engineering content, tips, and resources, so click the link in the description below to subscribe. Thanks!
One thing I’m hoping you can help me with is your fastener torque table. I see that you provide K values for various conditions of fasteners with the same materials as the thread they are being installed into. My question is: what should the K value be for stainless steel machine screws (18-8) installed into an aluminum tapped hole?
Many of the products I design are assembled using stainless fasteners but I have tapped aluminum holes, no inserts.
Looking for help with 8/32 stainless socket head cap screw (dry) into stainless part (dry). propper torque without galling.